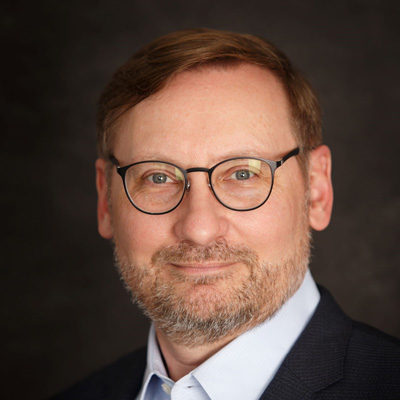
Dr Nathaniel Hentz
Director, Scientific Market Development, Artel
The COVID-19 pandemic means that it’s more important than ever to minimise sources of variability in the assay – or, quality control – process, and so lead to the design of a better, more robust product.
The vaccine sector is highly regulated, notes Dr Nathaniel Hentz, Director of Scientific Market Development at Artel, a company that offers products, services, and expertise to help life science labs meet their objectives for quality, productivity and compliance.
“Vaccine developers are obliged to follow regulations and established procedures,” he says. “The problem is, there is guidance for how to validate an assay, but no guidance is available to tell them how to build a proper assay; yet the quality of the assay is what drives the quality of the entire manufacturing process.
“If it isn’t done correctly it may mean a vaccine batch inappropriately passes or inappropriately fails. This could have a direct impact on patient safety, which is always the industry’s number one concern.”
Unfortunately, assays are only as good as the tools that are used to assemble them, and thus subject to different sources of variability.
“An assay is built using many components,” says Dr Hentz. “Take liquid handling, for example, a series of steps that move liquids from point A to point B. This can be done with an automated system, or by scientific staff pipetting by hand. But, if pipetting techniques are different — particularly if multiple analysts are working on the same assay in different laboratories — then operator to operator inconsistency can occur.”
Employing measuring tools, methods and training to minimise sources of variability
Liquid handling is just one source of variability in the assay process. Others include mixing, labware, plate-washing, time, temperature, etc.
However, measuring tools, methodologies and training are available to help labs understand and minimise all sources of variability.
“By using a process optimisation approach during assay development and validation, the entire assay process can be optimised to its fullest extent,” says Dr Hentz. “This can lead to the design of a much better, more robust assay.”
In the scramble to find a vaccine for COVID-19, assay optimisation and quality assurance is more important than ever.
“The increased manufacturing capacity requires more samples to be tested, which in turn increases opportunities for error and that can be a challenge for labs.
“Companies don’t want vaccine batches to fail because this costs them time and money and can impact the introduction to market and adoption of vaccination. Ultimately, it all comes back to patient health and safety, which is why companies are so keen to ensure product quality throughout the manufacturing process. Now, because of COVID-19, things are moving very fast, so it is important to minimise variability and any easy-to-fix mistakes.”
Artel works with labs helping them achieve assay development, liquid handling performance and operator training goals. For more information, please visit: artel.